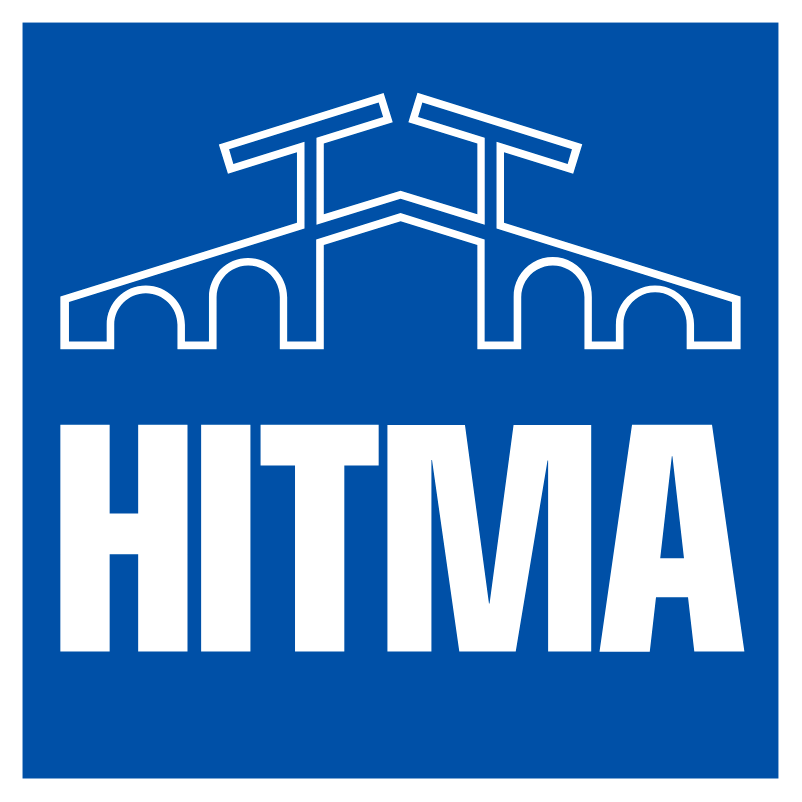
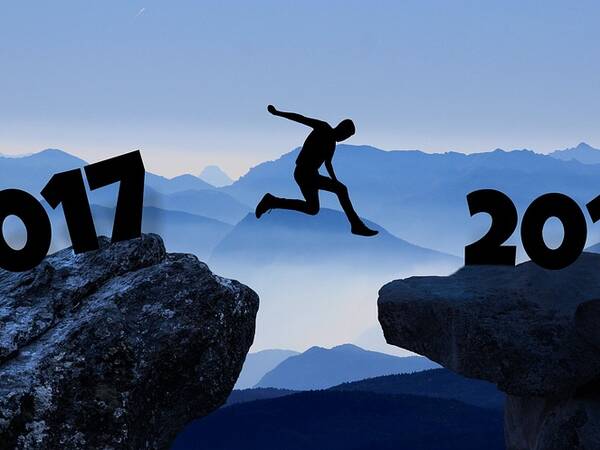
Will collaboration take single-use technology a step further in 2018?
I’m not one for traditions, but while writing this piece I realised that my annual ‘what-can-we-expect-to-happen-next-year-in-the-field-of-single-use’ blog is actually starting to look like a tradition. So once again I would like to put down on paper what I think will be the main developments in the (bio)pharmaceutical industry in terms of the use of disposable components and systems.
Lack of guidelines
Last year I wrote that the acceptance of single-use is being inhibited by the lack of guidelines. I believe that regulations should be introduced for the use of single-use components and systems. That way, everybody knows what they can expect from the manufacturers of single-use components and from the suppliers. In late 2016, I advocated creating a database with information about pressure tests and leachables and extractables for the various materials from which single-use products are manufactured.
Simplifying studies
To my regret, I have to admit that at the end of 2017 nothing has changed as far as setting up that database is concerned. As long as suppliers don’t join forces, it will never get off the ground. So the end users end up having to deal with the problems. And because they all have to tackle those problems on their own, nobody gets anywhere. Here and there, you do see ‘clubs’ being formed that say they are going to tackle these problems, but up to now there have been no significant successes. I think it’s possible to simplify the studies for the various end users. As far as I can see, the regulations have the power to do that. The FDA, therefore.
Sharing information
For the pharmaceutical industry, that simplification would be a step in the right direction. Pharmaceutical companies are now interpreting risk analyses themselves. Every man for himself. And information isn’t being shared in the sector. Suppliers of single-use components have to juggle with different agreements, guidelines and requirements for each customer. Manufacturers of single-use products have to make choices in order to comply with these agreements, guidelines and requirements as effectively as possible. The result? Products are more expensive and delivery times are longer.
Advantages of standardisation
Besides clear guidelines, standardisation also has certain advantages. I already wrote about this last year. It would be ideal for the end user if all single-use connectors were interchangeable without having to be validated every time. And by choosing sterile couplings as the materials, we avoid endless discussions. In this way, we safeguard the safety and quality of pharmaceutical processes. It also has a positive effect on the price of single-use products.
But we also still have a long way to go as far as this point is concerned. But I see that people are cautiously looking into the standardisation of transfer sets, consumables and tube sets with particular connectors. If these items were standardised, that would save a huge amount of production time. Pharmaceutical companies that succeed in standardising save costs because they themselves no longer have to perform any assembly tasks.
Knowledge and help
Standardisation also simplifies the processes of the pharmaceutical company. And yet I see many customers, completely unnecessarily, still using different sizes of tubing due to different production components. There seems to be a reluctance to change this. People are afraid of the risks and they can’t stand the thought of testing and validating again. Too little time and limited staff also play a role here. With the practical knowledge we have gained at Hitma, we can help companies with these types of standardisation procedures.
Outsourcing the assembly
One additional advantage of standardisation is that pharmaceutical companies no longer have to maintain their own assembly departments. As a result, external parties such as UltraPure International are starting to perform the assembly tasks for them. As part of that process, plug-and-play products are being developed with the advantage that you don’t need to autoclave them. That in turn results in cost savings, partly because components for autoclaving (such as filters) are no longer necessary. Ending up in a reduction in direct and indirect costs.
Less waste
Lastly, I see that more attention is being paid to reducing the amount of waste in the industry. I expect more research to be carried out into methods to limit waste from single-use components or possibly to recycle them. Given the Government programme ‘A Circular Netherlands by 2050’, this is a logical development. The goal is to save our raw materials and the environment and reduce CO2 emissions.
My prediction for 2018 is therefore that things are really going to start moving in this area. Especially among those end users who want to achieve standardisation, ease of use and cost savings. Unfortunately, the manufacturers of single-use components and systems haven’t yet joined forces and we’re also still waiting for the regulations to take shape.
I’ll get back to you if there are any changes in the meantime.