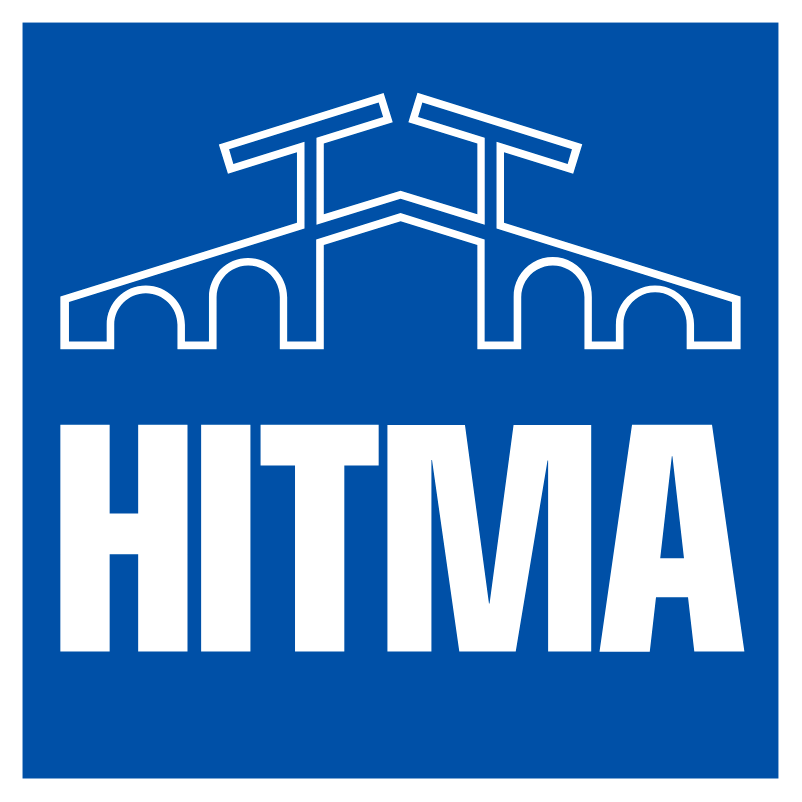
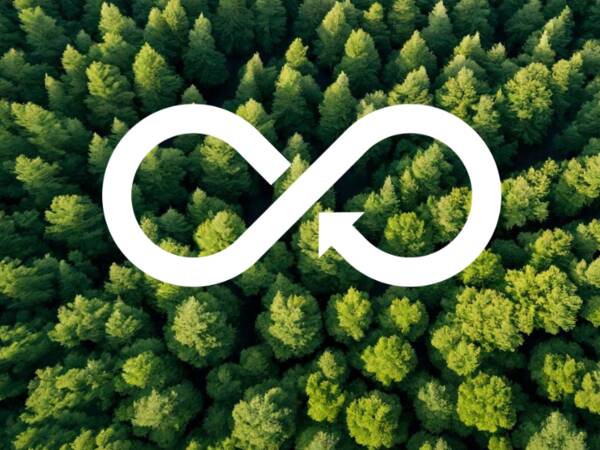
In today's (bio)pharmaceutical and biotechnology market, balancing between sustainability, safety and flexibility is important. The use of single-use components and assemblies that Hitma offers contributes positively to this. The transition to single-use systems is not only a step forward in reducing environmental impact of traditional systems such as stainless steel (SS), but also in ensuring product integrity by reducing the risk of contamination and leaks. In addition, single-use systems are currently the cheapest option for many start-ups, as well as in certain processes of larger companies.
Sustainability
The environmental impact of single-use systems differs from that of traditional SS systems. Research from 2009 (Rawlings & Pora) shows that stainless steel systems consume a relatively large amount of energy due to their sterilization and cleaning. However, for the use of materials, the single-use systems score much higher. Ultimately, this study showed that the energy consumption of multiple-use systems was generally almost 50% higher. This is an important consideration for (bio)pharmaceutical companies that are bound by regulations to certain standards but strive for greener production methods. There is still a world to be gained here, for example by recycling surplus, unused components or using more sustainable materials such as bioplastics.
Safety
Contamination is a major concern in the (bio)pharmaceutical and biotechnology sector. With stainless steel, a specific cleaning protocol must be used, adapted to the reactor or system for which it is used. Operators must be trained to properly implement these protocols without causing contamination or overlooking cleaning agent residues. In addition, all connections to the stainless steel devices must be made correctly, meaning without the risk of contamination or leaks. This should be done in clean areas with special facilities for air purification and cooling and heating, among other things. Research showed that these clean rooms are the biggest energy guzzlers and therefore have a lot of environmental impact.
Single-use systems significantly reduce the risk of cross-contamination because each component is used only once and then replaced. This ensures a high degree of product integrity and meets the strict industry standards. In addition, several single-use components can be assembled externally into one so-called assembly instead of assembling the system yourself in-house. This is done by trained operators at specialized parties, which also reduces the risk of incorrect connections. This is also done in clean rooms, but they are often used for longer periods of time and are therefore used more efficiently than the clean rooms at companies. This could further reduce the environmental impact of single-use systems.
The speed at which new solutions can be implemented is high and it gives companies the opportunity to respond quickly to market changes and social developments.
Flexibility
The developments within single-use technology are remarkable. New materials and designs provide improved performance and flexibility. The speed at which new solutions can be implemented is high and it gives companies the opportunity to respond quickly to market changes and social developments as we have seen during the last pandemic. It allows them to quickly switch between different production processes without much downtime and to produce smaller batches. This is especially important in a rapidly changing market where time-to-market is an important factor and a major advantage over multiple-use systems. These come into play when scaling up to larger production volumes and are therefore more of a long-term option.
Hitma and UltraPure International
The collaboration between Hitma and sister company Ultrapure International (UPI) ensures seamless integration of single-use assemblies into existing processes. With UPI's expertise in production and the product and market knowledge of single-use specialists Hitma, customers can rely on high-quality, sustainable and cost-effective solutions. We not only think about the design, but also take the expected forecast and the planning of deliveries into account in order to reduce any waste flows.
The future of (bio)pharmaceutical and biotechnological production lies in single-use technologies. By reducing costs, increasing efficiency and promoting sustainability, Hitma and Ultrapure International are committed to delivering innovative solutions that meet the needs of this dynamic market.