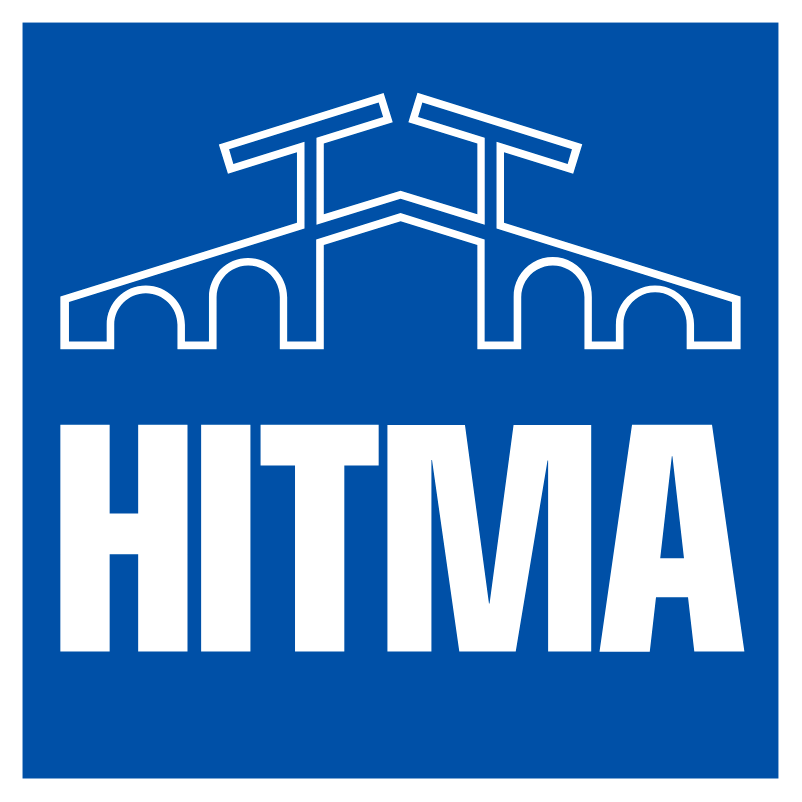

Ensuring sterility, quality and flexibility in syringe filling at hospital pharmacies through plug-and-play assemblies
More and more hospital pharmacies are choosing to fill syringes with medication using machines. Machine filling ensures accurate dosing and minimizes the risk of contamination, as the process can be conducted under sterile conditions and manual actions are reduced to a minimum. This automation is particularly important in hospital environments where patient safety is critical, especially since the medications are administered directly into the body.
Still, contamination risks may occur when the tubes, bags and connectors used to get the medication from the preparation vessel to the filling needle are manually connected. Sterility issues can also arise between the manual assembly of the components and their usage for filling syringes. The tubing, bags and connector materials also need to be compliant with quality regulations like cGMP and USP Class VI.
Plug-and-play assembly for syringe filling
A solution to these sterility, quality and flexibility issues is a plug-and-play single-use assembly. The tubing and bags can be pre-assembled into a dedicated syringe filling assembly. We have implemented this solution in hospitals like the Isala Ziekenhuis in Zwolle and the Catharina Ziekenhuis in Eindhoven.
This assembly eliminates the need for pharmacists to manually assemble tubing, bags and connectors. As a result, you minimize possible errors and save time on assembly, sterility and quality checks. We understand that every application is unique, so the syringe filling assembly will always be tailored to your specific needs and requirements.
Sterility
The main advantage of the plug-and-play syringe filling assembly in terms of sterility is that no manual labor is required, which minimizes sterility loss and contamination risk. The assembly is delivered gamma-irradiated, so that it does not need to be autoclaved in the hospital pharmacy. The fluid transfer assemblies are made in a cleanroom at our partner UltraPure International following validated procedures. If desired, a sterility claim can be provided for the gamma-irradiated assemblies.
Quality
The use of a single-use assembly also helps you to comply with strict quality regulations. At Hitma, we work with high-quality, controlled and certified materials. All of the assembly’s components are qualified for use in cGMP environments and made from materials that comply with USP Class VI and have known extractables profiles. In some cases, the desired sizing for the assembly is so complex that an overmolded design is chosen. In such cases, the double Y (the piece of tubing that fits in the peristaltic pump) is made from a single piece of silicone. This reduces the risk of leaks and loss of sterility on the connection to zero.
Flexibility
Because of our ability to manufacture custom assemblies, we can design the most suitable syringe filling assembly for your process. You can provide your own drawing, or have one of our specialists design it based on your application. After the design is approved, we can then produce the assembly in any desired quantity, with good lead times. The syringe filling assembly is manufactured by UltraPure International who have extensive knowledge of, among others, the Groninger filling machine. Because of their brand independent approach, we are able to deliver flexible and high-quality assemblies. We did this before successfully at the Isala hospital and later on also at the Catharina hospital.
I am happy to support you in deciding what the best solution is for your syringe filling process. Do you want to discuss how we can maximize the sterility, quality and flexibility of your application? Feel free to contact me.