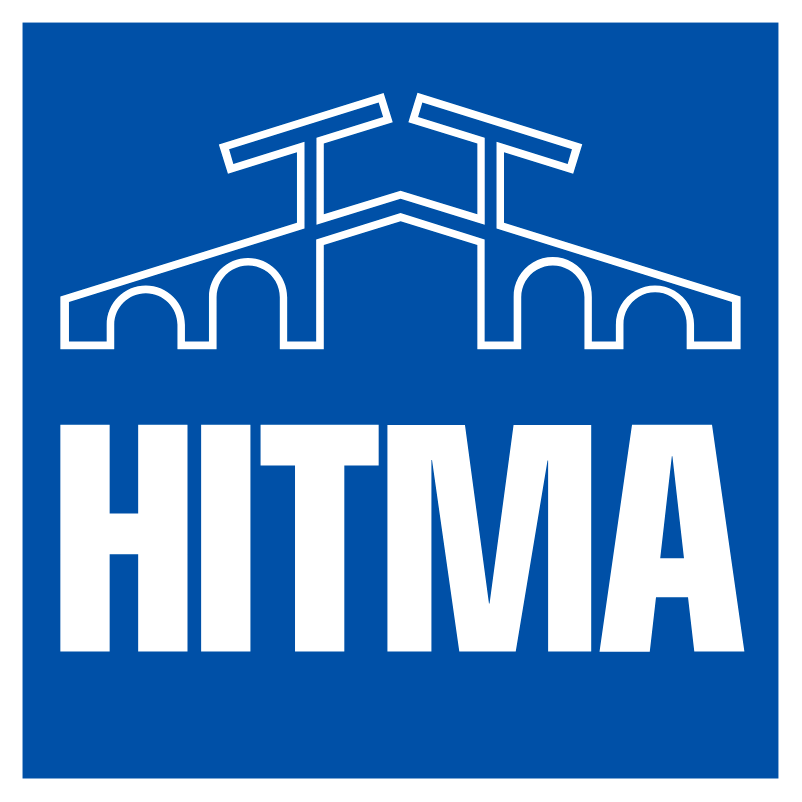
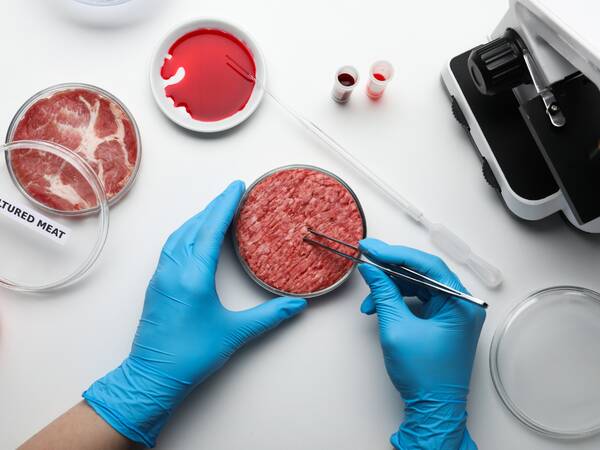
The protein transition is creating a more efficient, sustainable, safe, healthy, and animal-friendly food system with new revenue models. Government, universities, universities of applied sciences, foundations and companies are working closely together to encourage the shift to new kinds of protein, for example by developing novel protein sources and more efficient production systems.
I’m also noticing this shift toward cellular agriculture on a commercial level. Last year, the first cultivated meat tastings were held in the Netherlands. Companies like Meatable and Mosa Meat have secured large investments to scale up cultured meat production in a way that is kinder to animals and the planet. Tasters described the flavour of this meat as “quite normal.”
I see more developments like these that point to a promising future for cellular agriculture. The Netherlands, for instance, became the first EU country to set up a committee to evaluate cultivated meat tastings. The National Growth Fund is investing in Dutch cellular-agriculture infrastructure aimed at both fundamental research and commercial scale-up. Earlier we discussed how single-use technology can be applied in cellular agriculture. In this article, I’ll hone in on the sustainability, safety, scalability and compliance benefits of single-use assemblies.
Can sustainable cultivated meat become even more sustainable?
Single-use systems differ from traditional stainless steel systems in terms of environmental impact, and the most eco-friendly choice depends on the process. Single-use systems require less energy and water to manufacture than stainless-steel systems, but several single-use assemblies must be produced for every stainless steel system. Because single-use assemblies are suited to smaller batches, you can adjust how many systems are produced more precisely than with stainless steel. Their manufacture does generate considerable plastic waste, though. I’m seeing more and more initiatives to counter this plastic waste, like Hitma’s return and recycle service.
Stainless steel systems last far longer than single-use systems, yet they need frequent cleaning-in-place (CIP) and sterilisation-in-place (SIP), which consume large amounts of water and energy. Research by Rawlings & Pora (2009) has shown that multiple-use systems use, on average, 50% more energy than single-use systems. Combined with new recycling schemes, this means the CO2 footprint of single-use technology is lower – an important consideration for cultivated-meat producers who must meet regulatory standards but still aim for the greenest production methods.
Minimise the risk of operational issues
Cellular agriculture works with bacteria, yeasts, micro-algae and fungi, so sterility is essential. If components such as bioreactors and fermenters are not properly cleaned, cross-contamination can occur, leading to economic losses. Single-use assemblies are manufactured in a cleanroom and delivered read- to-use, reducing manual handling and the risk of error. Where necessary they can be gamma-irradiated or supplied in autoclave bags for on-site sterilisation.
Assembling separate single-use components yourself increases the risk of contamination through accidental exposure or manual mistakes. Just one little mistake, like a wrongly connected fitting, can cause cross-contamination. By using single-use assemblies that you replace after each batch, you minimise operational risks such as contamination and leakage.
Rapid scale-up for operational efficiency
Cellular agriculture looks set to be a fast-growing industry, though legislation can quickly intervene. As was the case when Italy’s government banned the production and sale of cultivated meat in 2023. To stay agile in such a turbulent market, it is vital to scale up rapidly without costly downtime. Single-use assemblies help minimise downtime: they are quick to implement and need no extensive cleaning or sterilisation between batches. They are therefore ideal for swiftly increasing production volumes and adapting processes to market demand. Reusable stainless-steel systems take longer to install and require far higher upfront investment, whereas single-use systems let you match the number of assemblies precisely to your production volume.
Compliance with cultivated meat regulations
The cultivated-meat industry is governed by strict rules on food safety, production processes and product quality to protect consumers of the products. Within the EU, cultivated-meat products must comply with rigorous Novel Foods legislation, which assesses all new foods for safety and health impact, including detailed requirements for sterile production, hygiene and product consistency. Producers must also meet Hazard Analysis and Critical Control Points (HACCP) standards, identifying critical control points (CCPs) in a quality manual and showing how these CCPs are managed to reduce contamination or other safety risks.
Our partner UltraPure International assembles and packages single-use assemblies in an advanced clean-room environment. Using these pre-validated and gamma-irradiated, autoclaved, or cleanroom-produced assemblies ensures compliance with strict regulations and saves the time normally spent re-validating systems, while minimising the risk of human error or incomplete cleaning.
Single-use assemblies can boost the sustainability, safety, efficiency and compliance of a cultivated-meat process. The most suitable assembly differs from one process to another. Curious to know which single-use assembly fits your process best? Or do you have questions about single-use technology in cellular agriculture? Feel free to contact me.